The items we will discuss in this chapter are:
Speed accuracy/smoothness/life and maintainability/dust generation/efficiency/heat/vibration and noise/exhaust countermeasures/use environment
1. Gyrostability and accuracy
When the motor is driven at a steady speed, it will maintain a uniform speed according to inertia at high speed, but it will vary according to the core shape of the motor at low speed.
For slotted brushless motors, the attraction between the slotted teeth and the rotor magnet will pulsate at low speeds. However, in the case of our brushless slotless motor, since the distance between the stator core and the magnet is constant in the circumference (meaning that the magnetoresistance is constant in the circumference), it is unlikely to produce ripples even at low voltages. Speed.
2. Life, maintainability and dust generation
The most important factors when comparing brushed and brushless motors are life, maintainability and dust generation. Because the brush and commutator contact each other when the brush motor is rotating, the contact part will inevitably wear out due to friction.
As a result, the entire motor needs to be replaced, and dust due to wear debris becomes a problem. As the name suggests, brushless motors have no brushes, so they have better life, maintainability, and produce less dust than brushed motors.
3. Vibration and noise
Brushed motors produce vibration and noise due to friction between the brush and the commutator, while brushless motors do not. Slotted brushless motors produce vibration and noise due to slot torque, but slotted motors and hollow cup motors do not.
The state in which the axis of rotation of the rotor deviates from the center of gravity is called unbalance. When the unbalanced rotor rotates, vibration and noise are generated, and they increase with the increase of the motor speed.
4. Efficiency and heat generation
The ratio of the output mechanical energy to the input electrical energy is the efficiency of the motor. Most of the losses that do not become mechanical energy become thermal energy, which will heat up the motor. Motor losses include:
(1). Copper loss (power loss due to winding resistance)
(2). Iron loss (stator core hysteresis loss, eddy current loss)
(3) Mechanical loss (loss caused by friction resistance of bearings and brushes, and loss caused by air resistance: wind resistance loss)
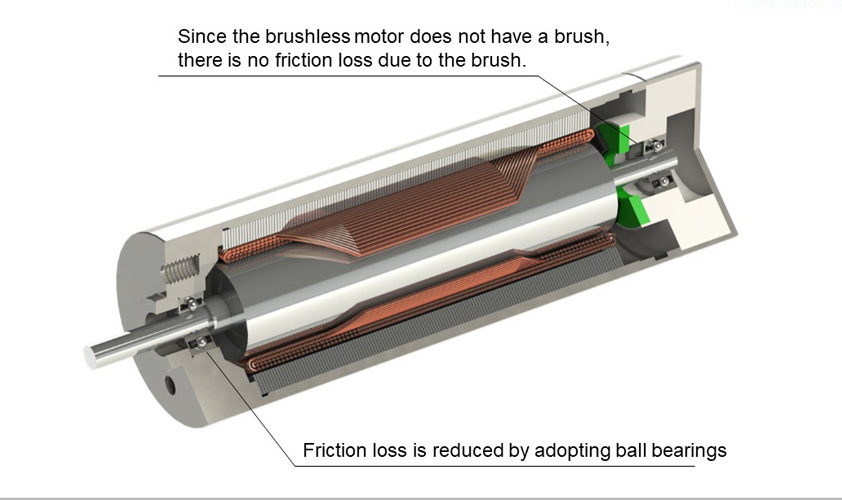
Copper loss can be reduced by thickening the enamelled wire to reduce the winding resistance. However, if the enamelled wire is made thicker, the windings will be difficult to install into the motor. Therefore, it is necessary to design the winding structure suitable for the motor by increasing the duty cycle factor (the ratio of conductor to the cross-sectional area of the winding).
If the frequency of the rotating magnetic field is higher, the iron loss will increase, which means that the electric machine with higher rotation speed will generate a lot of heat due to the iron loss. In iron losses, eddy current losses can be reduced by thinning the laminated steel plate.
Regarding mechanical losses, brushed motors always have mechanical losses due to the friction resistance between the brush and the commutator, while brushless motors do not. In terms of bearings, the friction coefficient of ball bearings is lower than that of plain bearings, which improves the efficiency of the motor. Our motors use ball bearings.
The problem with heating is that even if the application has no limit on the heat itself, the heat generated by the motor will reduce its performance.
When the winding gets hot, the resistance (impedance) increases and it is difficult for the current to flow, resulting in a decrease in torque. Moreover, when the motor becomes hot, the magnetic force of the magnet will be reduced by thermal demagnetization. Therefore, the generation of heat cannot be ignored.
Because samarium-cobalt magnets have a smaller thermal demagnetization than neodymium magnets due to heat, samarium-cobalt magnets are chosen in applications where the motor temperature is higher.
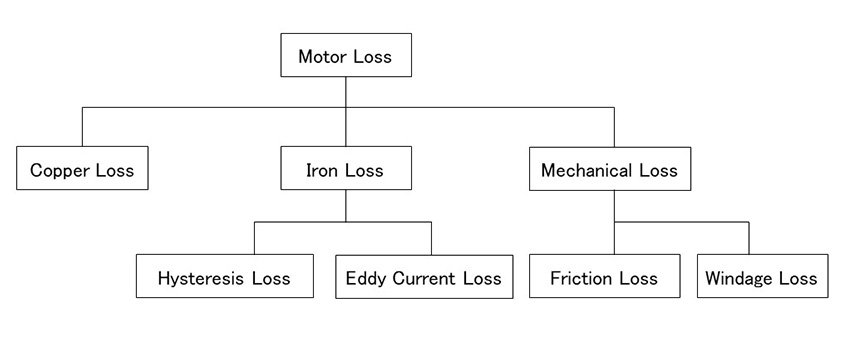
Post time: Jul-21-2023